滾動(dòng)軸承材料及熱處理之“熱處理技術(shù)進(jìn)展”
滾動(dòng)軸承材料及熱處理之“熱處理技術(shù)進(jìn)展”
- 2020/5/20 14:49:28
1、常規(guī)淬回火
高碳鉻類軸承鋼通常采用馬氏體淬回火,國(guó)內(nèi)外進(jìn)行了大量的研究,近年來(lái)根據(jù)軸承應(yīng)用工況,提出了一些針對(duì)性的研究與應(yīng)用。
ЧЕРМЕНСКИ.О.Н研究了不同溫度回火后硬度對(duì)軸承性能的影響。當(dāng)軸承載荷產(chǎn)生的接觸應(yīng)力超過(guò)σn0(σn0=2.57σ0,σ0為在單向拉伸或壓縮時(shí)開始塑性變形的應(yīng)力,取σ0.005),在計(jì)算可靠性要求不高的軸承壽命時(shí),硬度在58~64HRC范圍內(nèi)壽命的變化可以忽略不計(jì)。對(duì)于精密重載部件用球軸承,不允許在工作過(guò)程中因微塑性變形積累而使套圈溝道尺寸發(fā)生變化,最好采用高溫回火(200~250 ℃);對(duì)一般用途的軸承,最好的回火溫度不是現(xiàn)在的150~160 ℃,而是提高到170~180℃,不降低壽命且承載能力有所提高。
日本學(xué)者樋口博和對(duì)汽車變速箱軸承提出了3種長(zhǎng)壽命熱處理措施:1)增加殘余奧氏體以提高滾動(dòng)疲勞壽命(TM處理),對(duì)高碳銘軸承鋼進(jìn)行淬火時(shí),通過(guò)提高淬火溫度增加殘余奧氏體含量。2)提高回火軟化抗力(TA處理),進(jìn)行碳氮共滲時(shí),由于氮在表層的擴(kuò)散導(dǎo)致殘余奧氏體量增多,此外由于氮的固溶,回火軟化抗力上升,進(jìn)而提高疲勞壽命。3)晶粒微細(xì)化(FA處理),使鋼材的晶粒尺寸微細(xì)化,縮小到傳統(tǒng)材料晶粒尺寸的50%以下,以提高疲勞強(qiáng)度,并組合碳氮共滲處理實(shí)現(xiàn)進(jìn)一步長(zhǎng)壽命化。
GHEORGHIES.C,STEFANESCU.I.I對(duì)高碳鉻軸承鋼在磁場(chǎng)中進(jìn)行淬回火后的組織和性能進(jìn)行了研究。在磁場(chǎng)中進(jìn)行熱處理時(shí),馬氏體晶粒變小且組織均勻,殘余奧氏體減少,硬度可提高(1~2)HRC,抗彎強(qiáng)度提高50%,疲勞可靠度提高(承載時(shí)組織不易變化)。
對(duì)高碳鉻軸承鋼在淬火后進(jìn)行深冷處理可以提高耐磨性。1)在深冷處理過(guò)程中,大量的殘余奧氏體向馬氏體轉(zhuǎn)變,在磨損過(guò)程中向碳化物提供強(qiáng)大的支承并抑制其脫落,阻止大的麻點(diǎn)形成;2)由深冷處理產(chǎn)生的細(xì)小碳化物析出并均勻分布,也是耐磨性提高的原因,深冷處理試樣中碳化物的分布比那些沒(méi)進(jìn)行深冷處理的均勻,且碳化物體積分?jǐn)?shù)更高;3)深冷處理提高了馬氏體的轉(zhuǎn)變率,使合金基體組織細(xì)化,從而達(dá)到細(xì)晶強(qiáng)化效果,有助于耐磨性的提高。對(duì)100Cr6試樣淬火后進(jìn)行-186 ℃×24 h的深冷處理,并進(jìn)行200 ℃回火,與未進(jìn)行深冷處理相比,試樣的硬度提高18%,耐磨性提高37%。
BARTARYA.G,CHOUDHURY.S.K對(duì)熱處理工藝參數(shù)對(duì)鋼球滾動(dòng)疲勞壽命的影響進(jìn)行研究,860 ℃加熱后具有合適的未溶碳化物數(shù)量及原奧氏體晶粒,進(jìn)行160 ℃回火后可獲得較高的疲勞壽命。鋼球的拋丸強(qiáng)化可以減少鋼球加工和軸承裝配時(shí)的表面損傷,但疲勞壽命會(huì)下降,振動(dòng)噪聲會(huì)增加。
BRYAN.A等研究了滾動(dòng)接觸疲勞過(guò)程中初始?xì)堄鄳?yīng)力對(duì)軸承鋼材料性能的影響,對(duì)M50制大鋼球(28.6~41.3 mm)進(jìn)行機(jī)械處理,在表面下700 μm內(nèi)得到初始?xì)堄鄩簯?yīng)力(-400 MPa),與未機(jī)械處理的球相比,初始?xì)堄鄩簯?yīng)力延緩了鋼中微觀塑性變形硬化和組織變化(次表面黑色腐蝕區(qū)及白色條帶的出現(xiàn)),有利于提高接觸疲勞壽命。
在常規(guī)淬火設(shè)備方面,主要是在減小淬火變形,提高淬火后材料的組織和硬度均勻性方面進(jìn)行研究應(yīng)用。如近年來(lái)在國(guó)內(nèi)推行的高壓氣淬技術(shù),可明顯減小淬火變形,且節(jié)能環(huán)保;連續(xù)式鹽浴淬火設(shè)備在國(guó)內(nèi)得到越來(lái)越多的應(yīng)用,通過(guò)調(diào)節(jié)鹽浴含水量,可控制冷速,適用于不同的零件尺寸,保證最小的淬火變形及最大的硬度均勻性,且通過(guò)有效的熱回收利用裝置回收清洗液中的鹽,實(shí)現(xiàn)少無(wú)排放和低能耗。
另外,隨著熱鍛套圈技術(shù)的進(jìn)步,提高了毛坯精度,普遍使用熱回收氮基保護(hù)氣氛球化退火,降低了能耗和工件脫碳。
2、貝氏體淬火技術(shù)
張福成等對(duì)近年來(lái)貝氏體淬火技術(shù)進(jìn)行了詳細(xì)的綜述。與馬氏體組織相比,在馬氏體轉(zhuǎn)變起始溫度(Ms點(diǎn))以上進(jìn)行等溫淬火處理獲得的下貝氏體組織在保留高硬度的同時(shí),兼具更高的韌性,同時(shí)表面為殘余壓應(yīng)力,使得貝氏體淬火軸承在某些應(yīng)用領(lǐng)域具有優(yōu)異的疲勞性能,因此適用于裝配過(guò)盈量大、服役條件差的軸承,如承受大沖擊載荷的鐵路、軋機(jī)、起重機(jī)等軸承,潤(rùn)滑條件不良的礦山運(yùn)輸機(jī)械或礦山裝卸系統(tǒng)、煤礦用軸承等。高碳鉻軸承鋼貝氏體等溫淬火工藝已在鐵路、軋機(jī)軸承上得到成功應(yīng)用,取得了較好效果。
近年來(lái)新發(fā)現(xiàn)的納米貝氏體組織,也稱為硬貝氏體組織、低溫貝氏體或超級(jí)貝氏體組織,在保留與馬氏體相當(dāng)硬度的同時(shí),具有比常規(guī)下貝氏體組織更高的韌性和相當(dāng)?shù)谋砻鏆堄鄩簯?yīng)力,具有更加優(yōu)異的耐磨性和滾動(dòng)接觸疲勞性能,納米貝氏體鋼在材料設(shè)計(jì)、微結(jié)構(gòu)調(diào)控等基礎(chǔ)理論研究方面得到了快速發(fā)展,推動(dòng)了其在軸承制造領(lǐng)域的應(yīng)用,在軸承上應(yīng)用具有的巨大潛力。
在20世紀(jì)90年代,SKF等公司開展納米貝氏體用鋼開發(fā),如SKF的755V,通過(guò)特殊的等溫淬火得到更均勻的納米下貝氏體,硬度增加的同時(shí)韌性也提高了60%,耐磨性提高了3倍。處理的套圈壁厚超過(guò)100 mm,近期將其應(yīng)用于高鐵軸承。國(guó)內(nèi)近十幾年也開展了納米貝氏體技術(shù)的研究,如張福成等團(tuán)隊(duì)開發(fā)的含Al,Si的全淬硬鋼及滲碳鋼,經(jīng)過(guò)貝氏體淬火后獲得納米貝氏體,接觸疲勞壽命較普通軸承鋼及滲碳鋼分別提高1倍、2倍以上。
在國(guó)內(nèi),納米貝氏體軸承技術(shù)的應(yīng)用仍有一些問(wèn)題,最突出的問(wèn)題是等溫處理時(shí)間過(guò)長(zhǎng),急需縮短熱處理工藝周期的方法。另外,服役過(guò)程中殘余奧氏體的轉(zhuǎn)變及其引發(fā)的尺寸穩(wěn)定性問(wèn)題,納米貝氏體組織在軸承服役過(guò)程中的組織演變規(guī)律及對(duì)服役壽命的影響,納米貝氏體軸承更適用的工況等,均有待深入研究。
3、碳氮共滲
高碳鉻軸承鋼的碳氮共滲處理是在添加了5%~15%丙烷和丁烷的滲碳?xì)夥罩屑尤牒橘|(zhì)(如氨氣),將碳和氮同時(shí)滲入擴(kuò)散到軸承鋼中的處理技術(shù)。由于在材料表層擴(kuò)散的氮元素會(huì)使奧氏體變得穩(wěn)定,因此淬火后殘余奧氏體量增多,而且通過(guò)氮元素的固溶作用提高了抗回火軟化性,亦增加了滾動(dòng)疲勞壽命。
KARTHIKEYAN.R等對(duì)52100鋼實(shí)施的碳氮共滲處理工藝及處理后的組織、硬度等進(jìn)行了詳細(xì)的研究。工藝曲線、成分分析、顯微組織、硬度分別如圖1—圖3所示。碳氮共滲溫度一般在A1以上,溫度越高則滲速越高,但滲后晶粒越粗,氮含量越低。碳氮共滲后除未溶碳化物外,還有大量細(xì)小的氮化物、碳氮化物,提高了硬度和耐磨性。另外滲層組織中有高含量的殘余奧氏體(20%以上)。因大量殘余奧氏體的存在,滲后低溫回火的硬度與未滲的相近,但在較高溫度回火后,滲層表面硬度明顯高于未滲件(如300 ℃回火后,滲后硬度為63.6HRC,未滲的僅58HRC)。
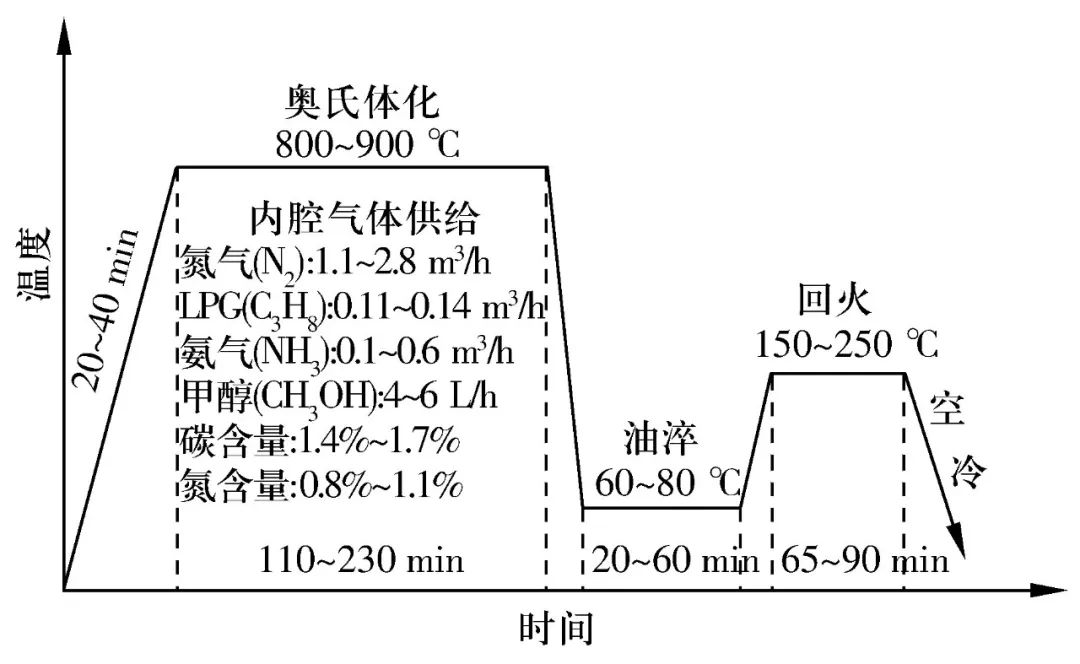
圖1 碳氮共滲工藝曲線
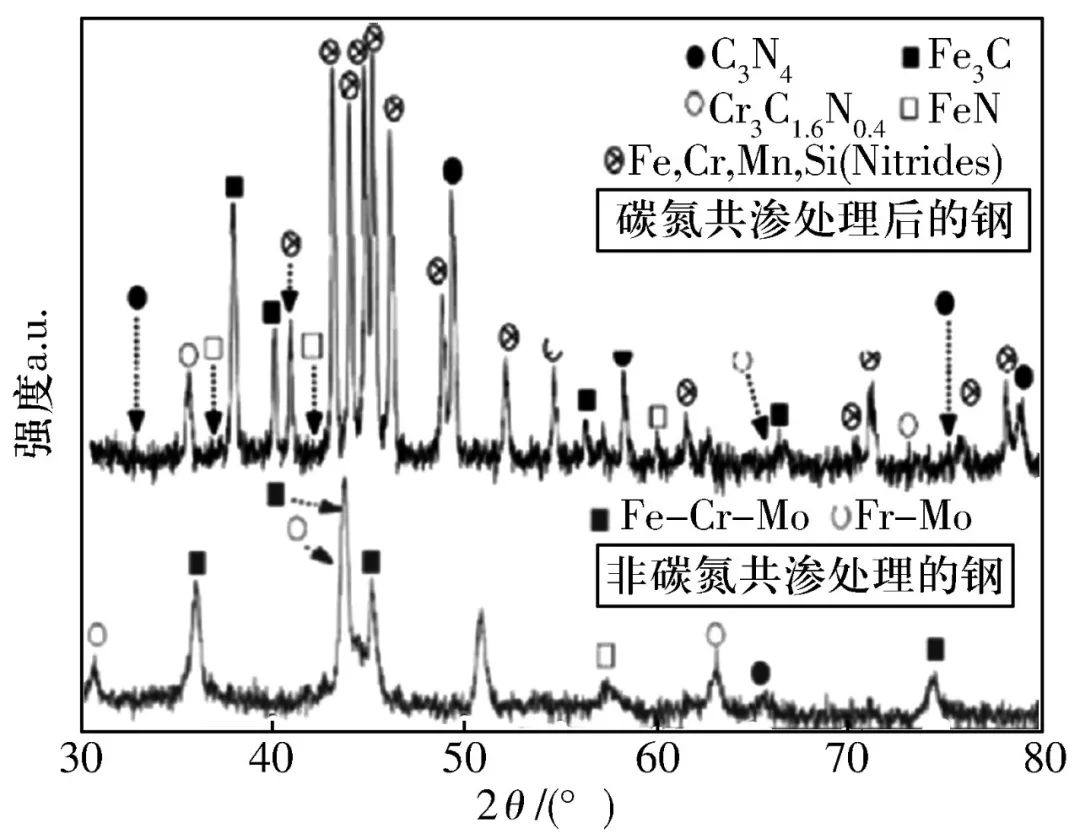
圖5 滲后表層X(jué)-射線衍射圖
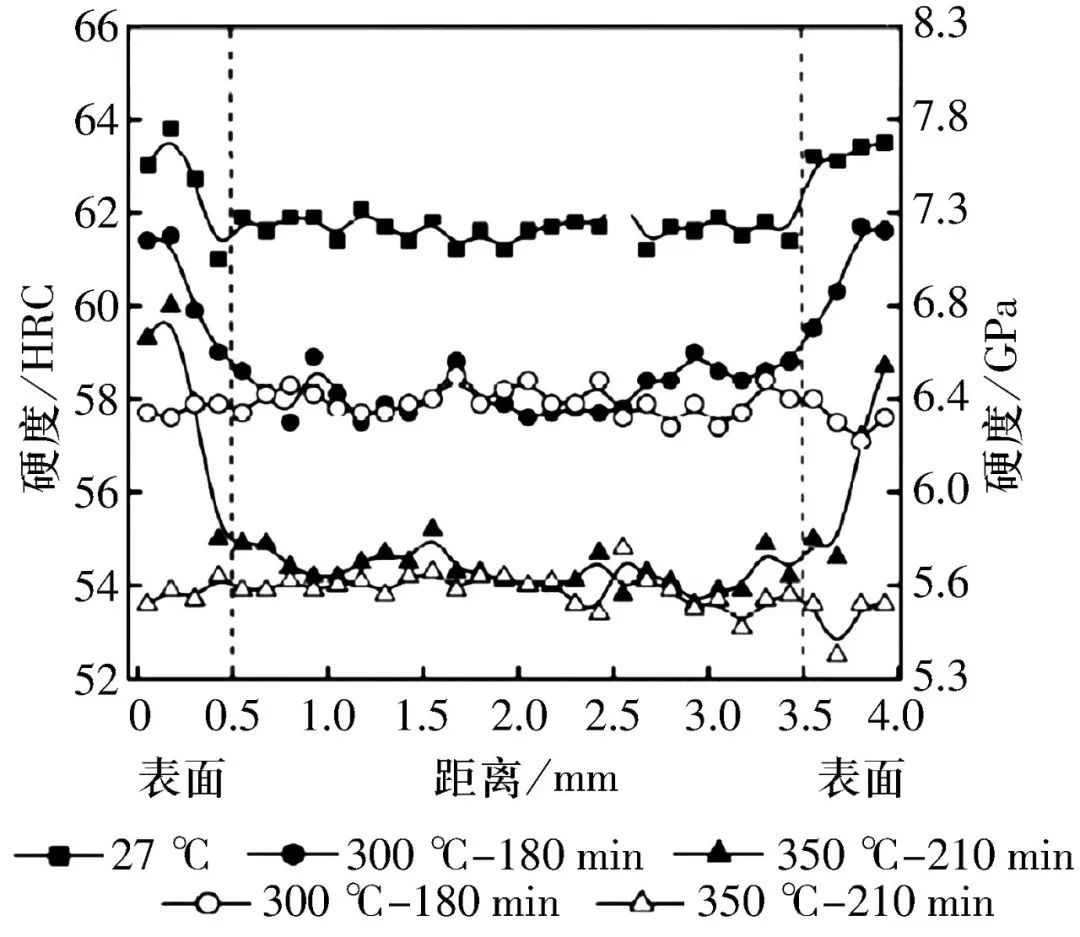
圖6 碳氮共滲和非熱處理鋼的硬度曲線
(實(shí)心符號(hào)代表碳氮共滲,空心符號(hào)代表非碳氮共滲)
DAISUKE.S等研究了高表面氮含量碳氮共滲SUJ2的滾動(dòng)接觸疲勞壽命。通過(guò)控制碳氮共滲氣氛的氮?jiǎng)菔固嫉矟B后成品內(nèi)圈的表面氮含量分別為0.1%和0.4%,并在人工壓痕及污染潤(rùn)滑的條件下進(jìn)行軸承疲勞壽命對(duì)比試驗(yàn)。人工壓痕條件下,高氮含量(0.4% N)的碳氮共滲軸承疲勞壽命分別約為常規(guī)碳氮共滲(0.1%N)的2倍及普通淬回火的3倍;污染潤(rùn)滑條件下則為普通淬回火的2倍。高的表面氮含量提高了熱處理后的殘余奧氏體含量,從而提高了軸承壽命。文中還對(duì)高氮碳氮共滲不同溫度回火后的壓痕深度進(jìn)行測(cè)量和計(jì)算,表明回火溫度越高,壓痕深度越淺,殘余奧氏體含量越低,但未對(duì)不同溫度回火后的疲勞壽命進(jìn)行對(duì)比。但可以推測(cè):對(duì)于潔凈潤(rùn)滑的軸承,采用高的溫度回火應(yīng)有利于提高硬度和耐磨性。
20世紀(jì)90年代起,日本各公司積極應(yīng)用這種特殊熱處理技術(shù),將其應(yīng)用于污染潤(rùn)滑條件下工作的軸承以提高壓痕起源型剝落壽命;應(yīng)用于乏油潤(rùn)滑條件下工作的軸承以提高耐磨性;應(yīng)用于異常白色組織剝落失效的軸承以防止早期剝落。
1981年,洛陽(yáng)軸承研究所開展了軸承鋼的碳氮共滲研究,并將碳氮共滲處理的軸承裝于機(jī)床進(jìn)行試驗(yàn),壽命明顯提高。但因種種原因被擱置,沒(méi)有推廣應(yīng)用。進(jìn)入21世紀(jì)后,國(guó)內(nèi)軸承企業(yè)開始積極推廣應(yīng)用這一技術(shù),尤其是在汽車變速箱軸承方面,已成為標(biāo)準(zhǔn)的熱處理工藝。
4、其他化學(xué)熱處理
XIE.L.C等研究了表面硬化技術(shù)和硬化層深度對(duì)AISI 8620,9310,4140鋼的滾動(dòng)接觸疲勞性能的影響。8620及9310采用氣體滲碳和真空滲碳,4140采用感應(yīng)淬火,得到不同硬度和硬化層深度。接觸疲勞試驗(yàn)表明,硬化層硬度越高、層深越厚(到613HV的最大深度小于1 mm),接觸疲勞壽命越長(zhǎng),滲碳處理大于感應(yīng)淬火,真空滲碳大于氣體滲碳;而且對(duì)應(yīng)于最大等效應(yīng)力深度(約0.13 mm)處的硬度與疲勞壽命強(qiáng)相關(guān),該處硬度越高,疲勞壽命越長(zhǎng)。
GLOECKNER.P等將薄層氮化應(yīng)用于M50,M50NiL制航空發(fā)動(dòng)機(jī)球軸承,提高表面硬度及殘余壓應(yīng)力,防止邊界潤(rùn)滑條件下滾動(dòng)接觸區(qū)內(nèi)微觀滑動(dòng)引起微剝落。
航空發(fā)動(dòng)機(jī)軸承運(yùn)行于高溫高速及污染潤(rùn)滑條件下,常常因污染潤(rùn)滑而失效,軸承長(zhǎng)壽命的措施之一是在常規(guī)熱處理后進(jìn)行離子氮化。YAGITA.K等對(duì)軸承零件用高合金鋼(M50,M50NiL)的等離子氮化處理進(jìn)行了研究。為保證在氮化后不出現(xiàn)有害的化合物層和晶間析出物,滲層中的C+N含量需小于1.7%,在430 ℃氮化10 h后進(jìn)行低于回火溫度的擴(kuò)散處理,在不降低心部硬度的前提下保證足夠的滲層深度。經(jīng)以上處理后,接觸疲勞試驗(yàn)所得的疲勞壽命L10提高了近7倍。
KOYO通過(guò)對(duì)SUJ2進(jìn)行特殊熱處理(碳氮共滲)開發(fā)了SH軸承,在表面獲得高的硬度和一定量的殘余奧氏體,使其在污染潤(rùn)滑條件下具有較高的壽命,且污染越嚴(yán)重,提高壽命的效果越顯著。
5、感應(yīng)加熱整體熱處理
感應(yīng)加熱淬回火有許多優(yōu)點(diǎn),如環(huán)保、可集成于生產(chǎn)線中,開、停機(jī)時(shí)間短等,一般用于表面淬火(如輪轂軸承),較少用于整體淬火。國(guó)內(nèi)企業(yè)只有洛陽(yáng)LYC將感應(yīng)加熱整體淬火用于308自動(dòng)線,原因是感應(yīng)加熱的選擇性難以保證整個(gè)零件的加熱均勻性,且擔(dān)心高溫短時(shí)加熱是否可重復(fù)性較好地控制碳在基體中的溶解量。
NTN開發(fā)了可控制鋼中溫度及顯微組織的整體感應(yīng)加熱淬回火技術(shù),其加熱控制系統(tǒng)如圖4所示。利用2支溫度計(jì)同時(shí)測(cè)量套圈內(nèi)外徑溫度,PID控制溫度,基于溫度測(cè)量結(jié)果的PC程序?qū)崟r(shí)預(yù)測(cè)材料的性能,當(dāng)鋼中未溶碳化物面積到達(dá)6%~10%時(shí)停止加熱,噴水淬火;根據(jù)每個(gè)回火溫度下回火時(shí)間與硬度的關(guān)系,采用類似的方法控制回火溫度及時(shí)間。對(duì)采用900 ℃感應(yīng)加熱淬火及230 ℃回火的套圈進(jìn)行性能測(cè)試,與爐內(nèi)加熱淬回火的標(biāo)準(zhǔn)軸承相比,硬度及均勻性、耐淺層剝落及涂抹性能與標(biāo)準(zhǔn)軸承相當(dāng),尺寸穩(wěn)定性及L10高于標(biāo)準(zhǔn)軸承,整個(gè)工藝每千克的CO2排放量由566 g降至318 g。
圖4 帶溫度控制的感應(yīng)加熱系統(tǒng)示意圖
NTN進(jìn)一步研究了感應(yīng)加熱條件對(duì)軸承鋼性能的影響。淬火溫度為900,950,1 000 ℃,目標(biāo)未溶碳化物面積為4%,8%,12%(采用不同加熱時(shí)間控制),回火為180 ℃×2 h,240 ℃×43.2 s,310 ℃×36.8 s。從尺寸變化率、額定靜載荷、靜態(tài)斷裂強(qiáng)度及剪切疲勞強(qiáng)度等性能考察不同熱處理?xiàng)l件的影響,認(rèn)為性能不低于爐內(nèi)處理的最合適的熱處理?xiàng)l件見(jiàn)表2。在合適熱處理?xiàng)l件下,軸承壽命可達(dá)基本額定壽命的4倍以上。
表1 適合JIS-SUJ2的感應(yīng)淬火條件